Direct Metal Laser Sintering (DMLS)

EOSINT M280
- 250x250x325 mm (9.8×9.8×12.8 in) build volume
- 20 μm layer thickness
- 400 W laser
- Heat treatment oven
- Abrasive polishing
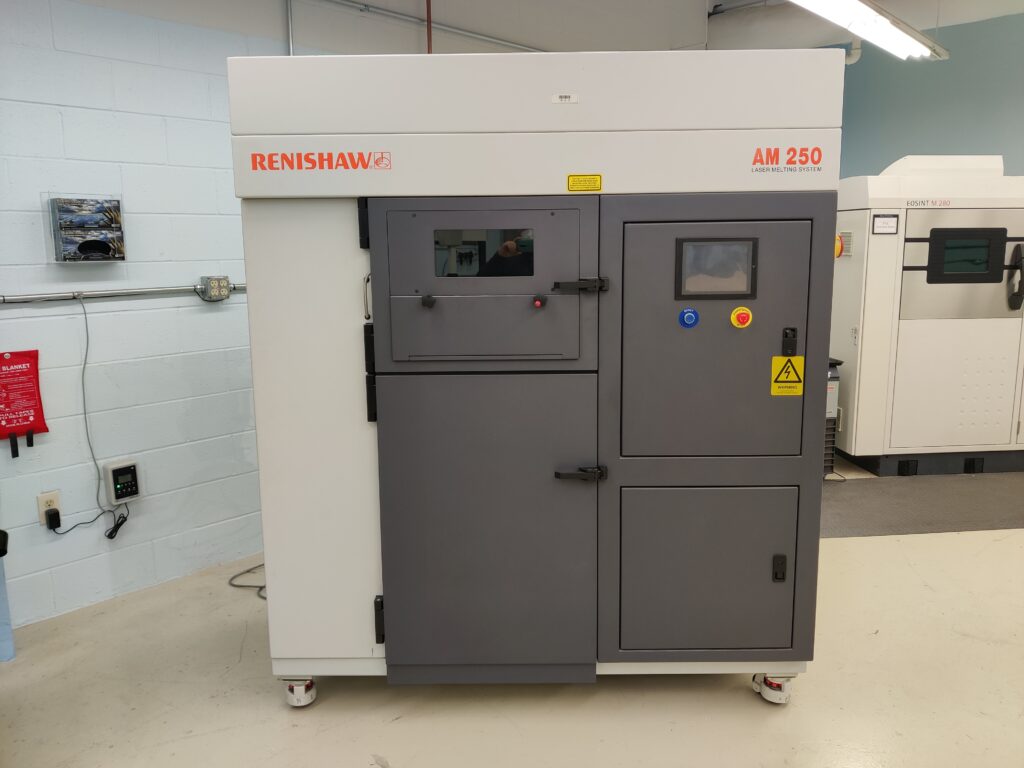
Renishaw AM250
- 250x250x300 mm (9.8×9.8×11.8 in) build volume
- 20 μm layer thickness
- 200 W laser
What is Direct Metal Laser Sintering?
DMLS functions in a similar way to polymer SLS, where a laser is used to selectively fuse layers of metal powder. Unlike polymer SLS, however, DMLS requires support structures for overhanging features. Due to the extreme temperatures associated with fusing the metal powders, large internal stresses can develop within DMLS parts. Post-build heat treatment is often used to mitigate the effects of the residual stresses and limit warping. Additional heat treatment such as hot isostatic pressing (HIP) may also be necessary to reduce the porosity within the sintered parts.
DMLS Advantages
- Near full density metal parts
- Complex internal and external geometric capabilities
- Wide range of material options
DMLS Considerations
- Avoid closed cavities or small openings that may prevent powder removal
- Support structures are required for overhangs that exceed 45 degrees
- Avoid internal overhanging geometries where support structures cannot be removed
- Feature sizes should be larger than 0.5 mm