Material Extrusion (ME)
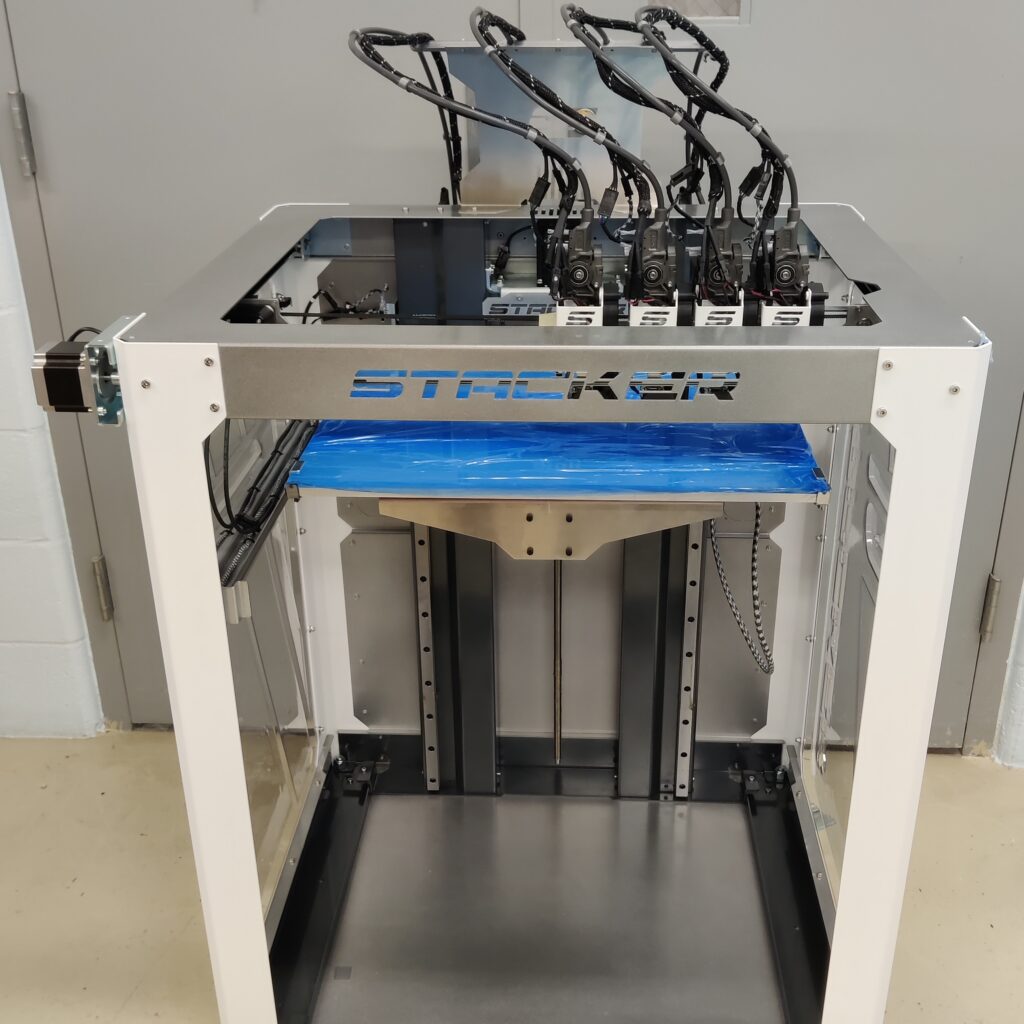
Stacker S4
- 345x520x650 mm (13.6×20.5×25.6 in) build volume
- 4 extruders for multi-material parts
- Open architecture
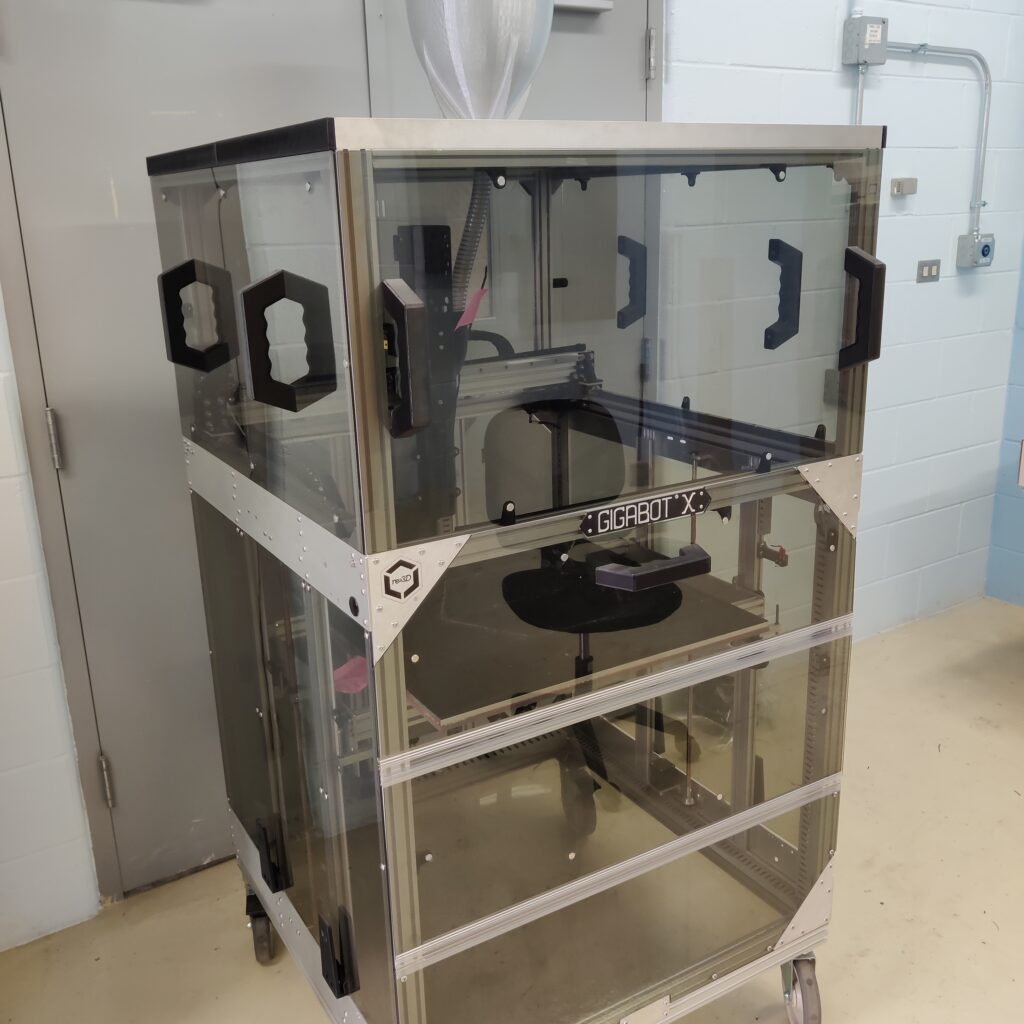
re:3D Gigabot X
- 565x593x470 mm (22.2×23.3×18.5 in) build volume
- Prints from pellets and flakes
- Ability to print from recycled materials
- On loan from re:3D for research
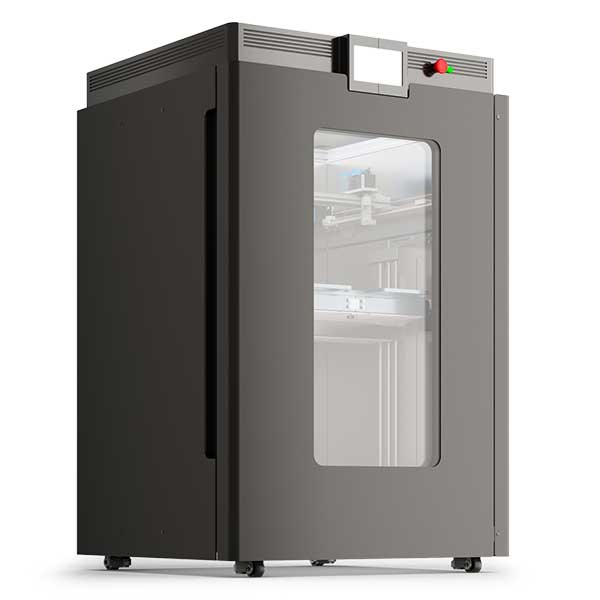
AON M2+
- 450x450x565 mm (17.7×17.7×22.2 in) build volume
- Dual 500 degree C extruders
- Ability to print high temperature materials such as PEEK, PEKK, and ULTEM
- Build chamber heating to 135 degrees C
What is Material Extrusion?
Material extrusion goes by several names including fused deposition modelling (FDM), fused filament fabrication (FFF), and fused granular fabrication (FGF). The basic principle for polymer material extrusion is to melt polymer feedstock and extrude it through a nozzle onto a build platform. The feedstock can be in the form of filament strands that are wound around a spool or granulated pellets that are fed to the extruder via a hopper. The liquid polymer cools as it exits the nozzle and solidifies, allowing the material to be selectively deposited. The cross section of the part is traced by the extruder for a given layer, and the process is repeated by lowering the build platform.
ME Advantages
- Wide range of material options
- Hollow internal cavities are possible
- Low waste
ME Considerations
- Support structures are required for overhangs that exceed 45 degrees
- Layers tend to be pronounced, causing rough external surfaces
- Feature sizes should be on the order of 1.0 mm for the best results
- Avoid printing large flat plates parallel to the build plate to avoid excessive warping