Selective Laser Sintering (SLS)

Sinterstation HiQ+HS
- 380x330x450 mm (14.9×12.9×17.7 in) build volume
- 100 μm layer thickness
- Nyln 11, Nylon 12, DuraForm Flex
What is Selective Laser Sintering?
SLS uses a laser to fuse layers of polymer powders. Thin layers of powder are spread across the build surface, and the laser scans the cross section of the part. The energy from the laser locally melts the polymer powders, fusing them together. The remaining unfused powder layer is self-supporting, thereby eliminating the need for support structures on overhanging features.
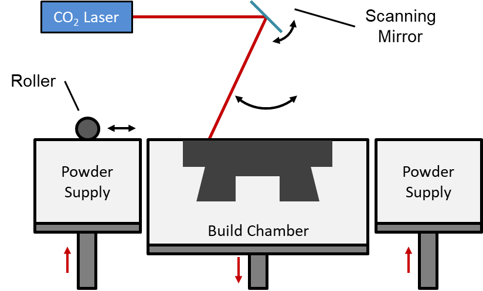
SLS Advantages
- Geometrically complex features
- Sacrificial support structures not necessary
- Near full density polymer parts
- Ability to nest many parts within a single build can reduce costs
SLS Considerations
- Avoid enclosed cavities or small openings that would prevent powder removal
- Features should be larger than 0.5 mm
- Avoid large flat features parallel to the build plane