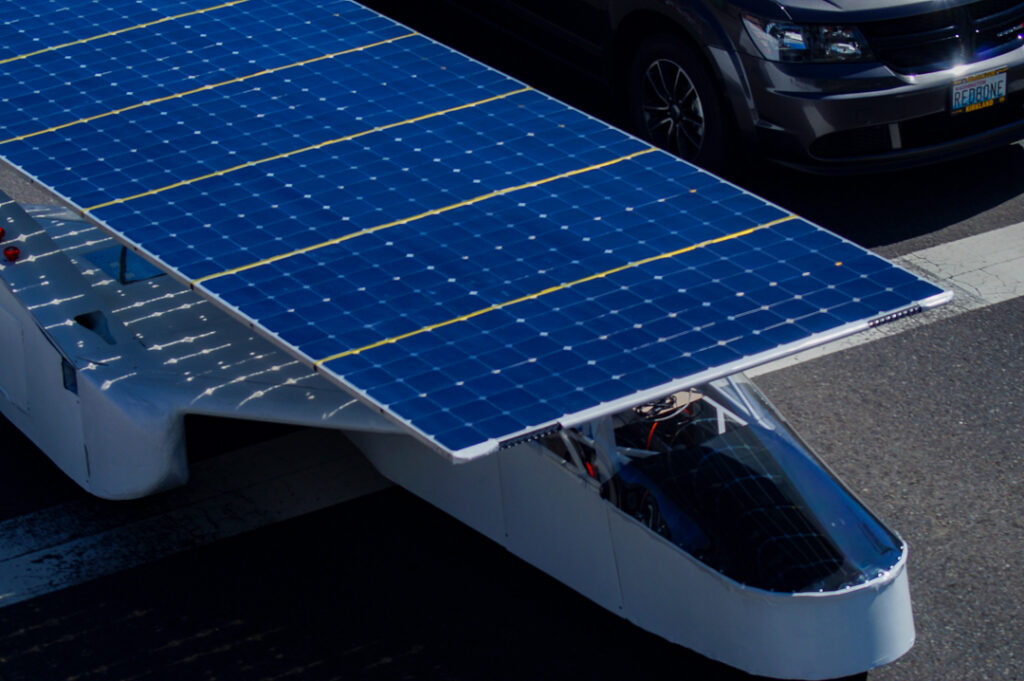
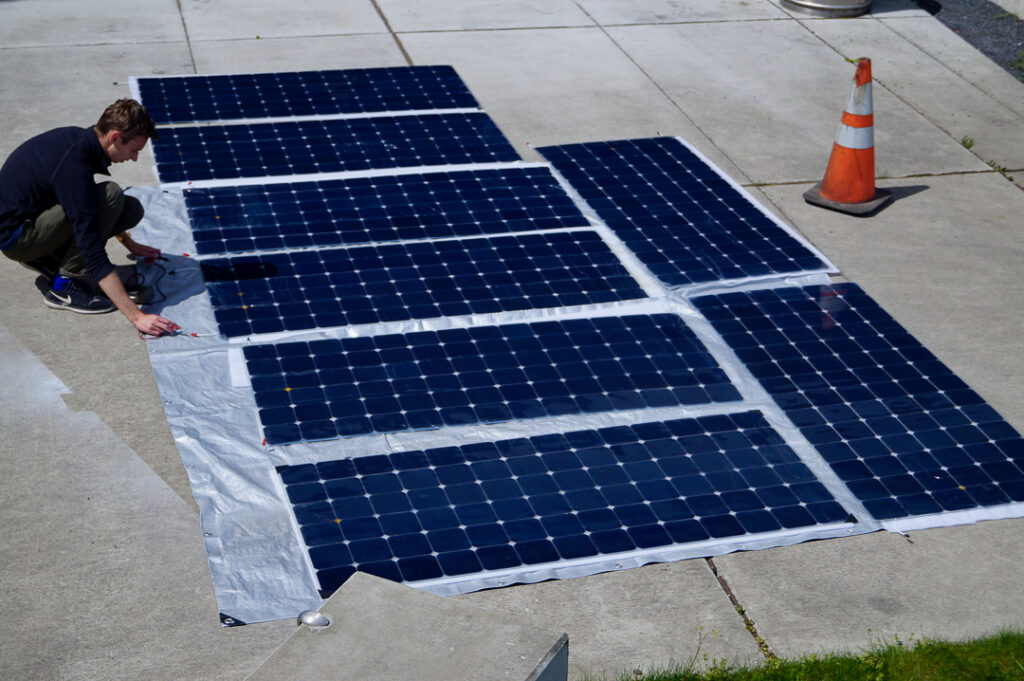
Solar panel redesign for 2nd solar car (solar panel 2.0)
When we designed our follow-up solar car in the 2019-2020 school year, we chose to integrate the solar panel flush with the body for improved aerodynamic performance. This reduced the available space for solar cells and introduced shade from the driver cockpit.
We learned more about the problems that uneven shading can cause in solar panels, – diode reverse bias, power dissipation, and heat generation – and also a solution for these problems, bypass diodes. We designed a new panel configuration with bypass diodes wired in parallel with strings of solar cells, especially near the cockpit, to reduce shading losses.
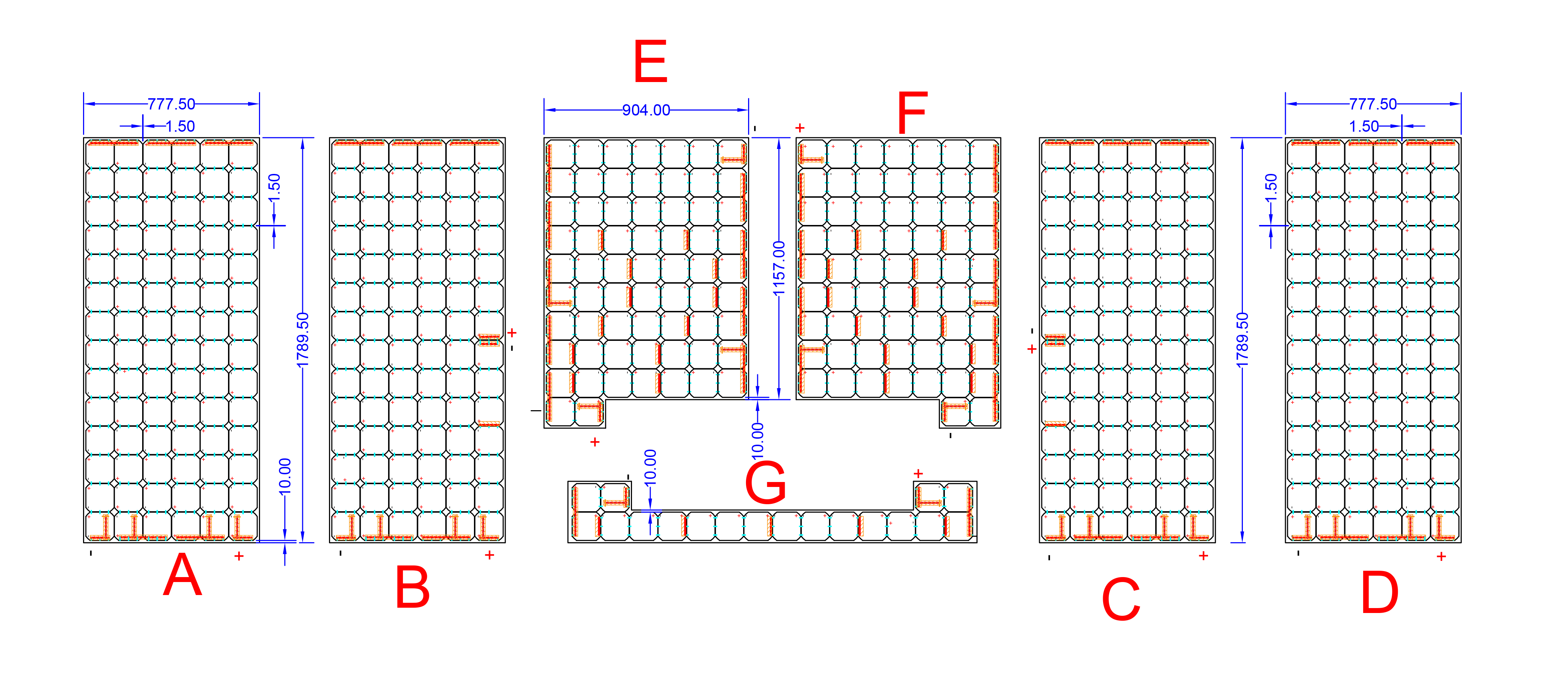
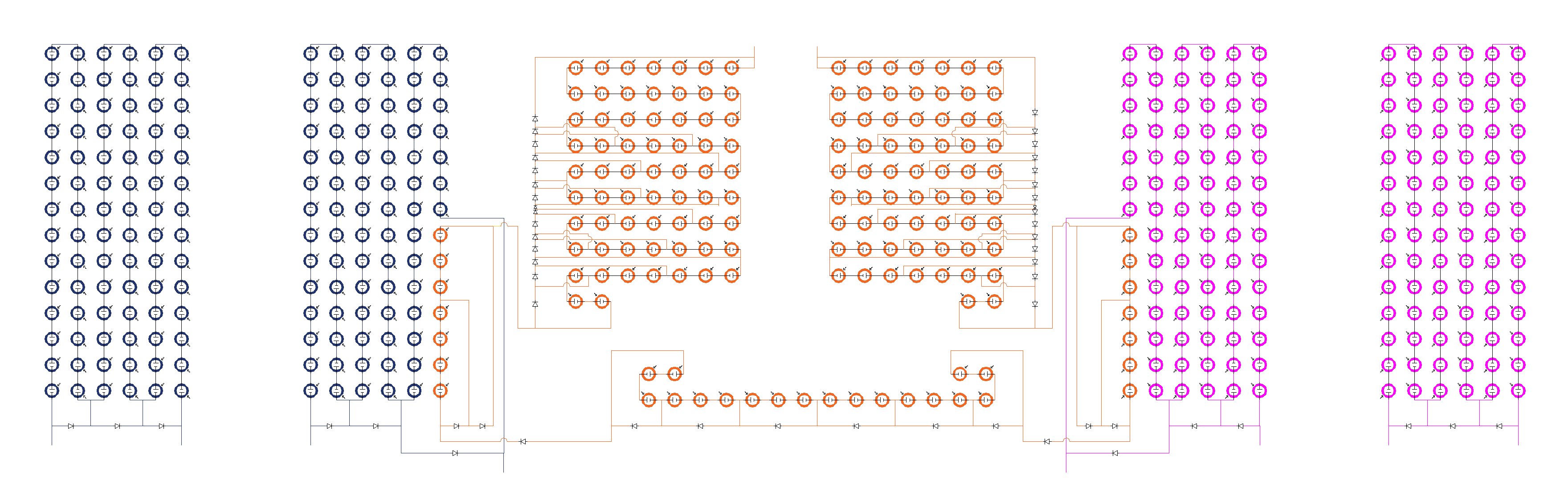
With our second car we also added greater driver control of the power systems, and improved safety features. Below is an updated schematic of the power systems.
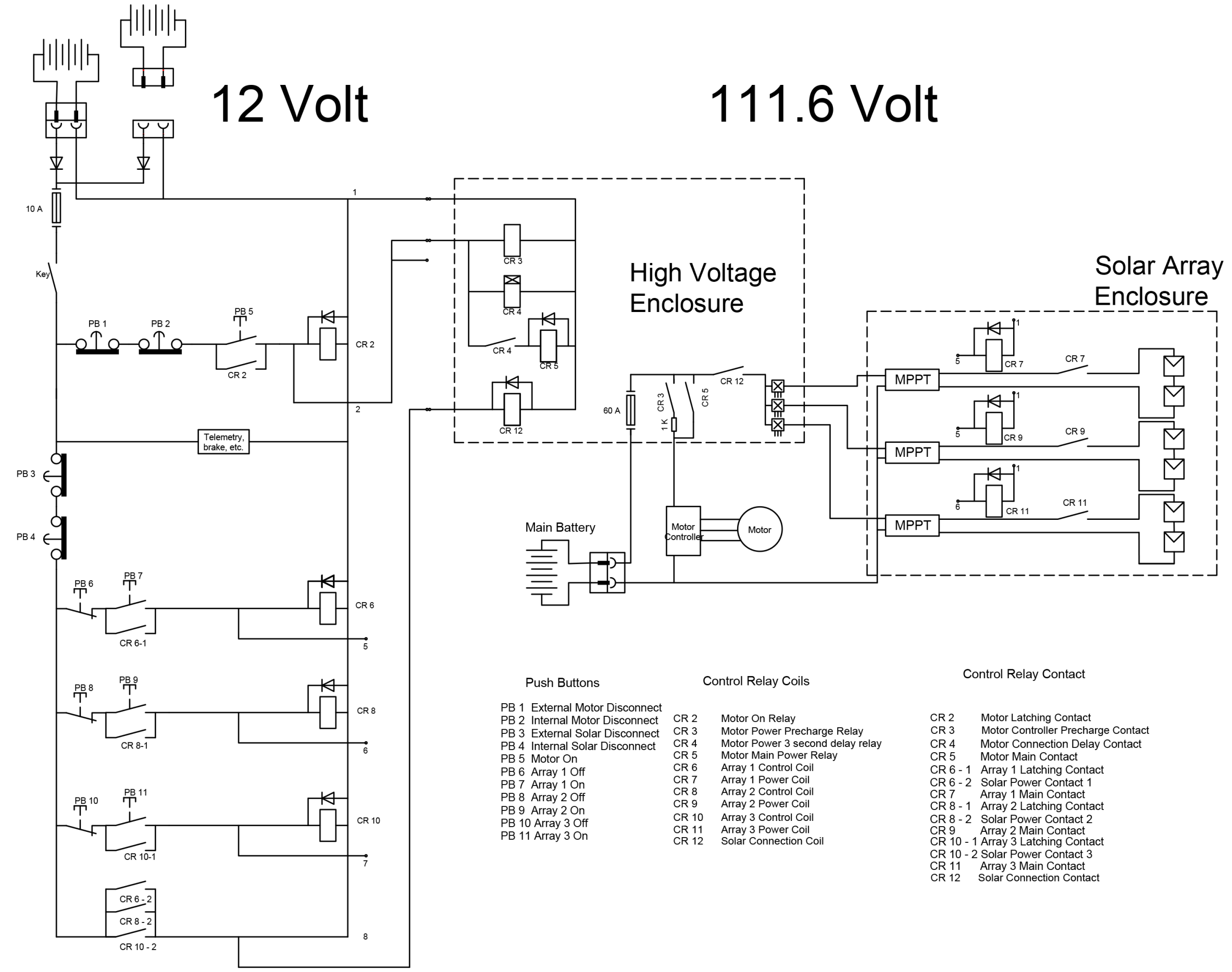
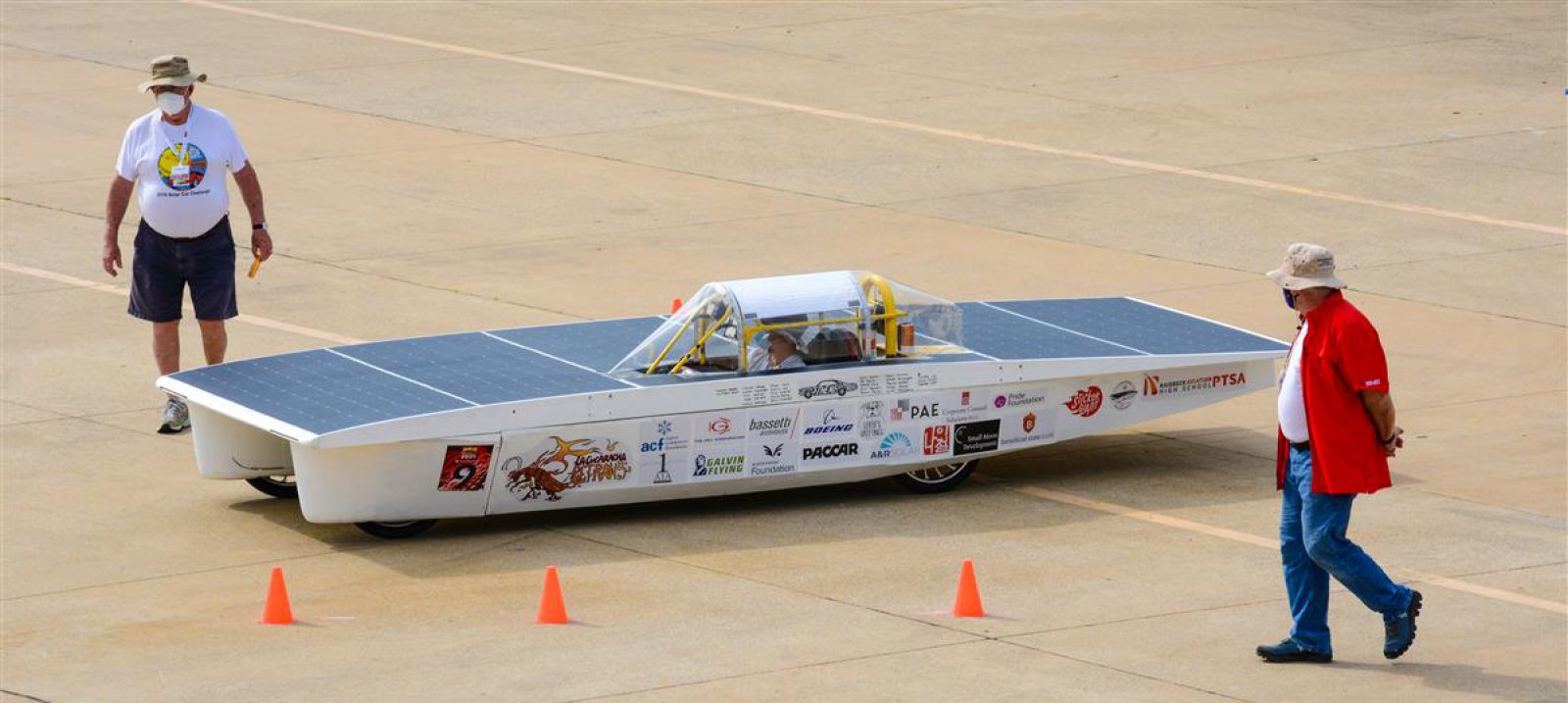
Solar Cell Investigation and Lamination Experiments
In the initial exploration stages of our solar vehicle design process, I researched the methods used by current teams to examine their feasibility with our design constraints (ease of manufacturing, available tools, budget, etc). With this we began hands-on prototyping with interconnection and lamination of Sunpower solar cells.
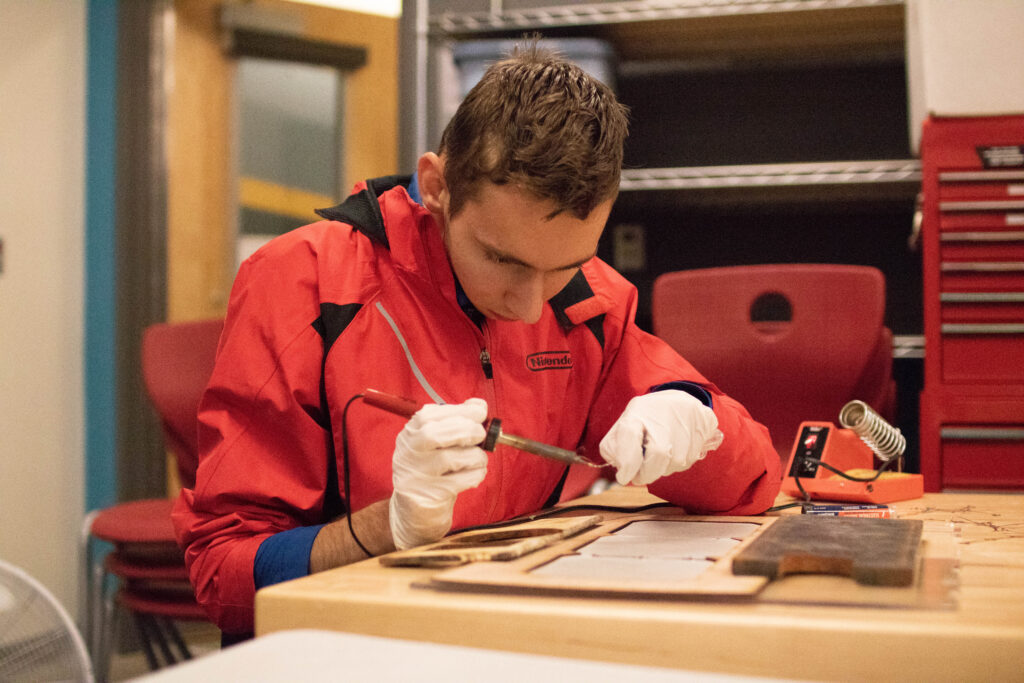
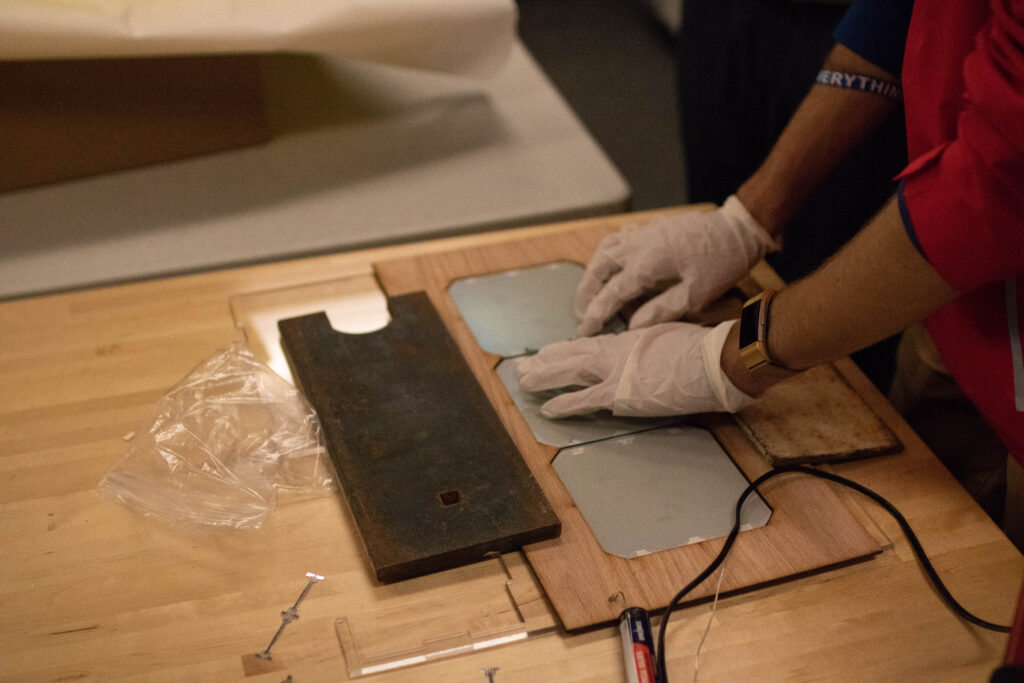
As high school students, lamination was a word we most associated with the preservation of paper materials and were curious if the lamination plastics used in schools would suffice for the preservation of the solar cells.
We found a problem rather quickly – as the laminate contracted upon heating, it trapped air, forming wrinkles and air bubbles. To fix this we would need the lamination to be coupled with a vacuum pump and an airtight seal.
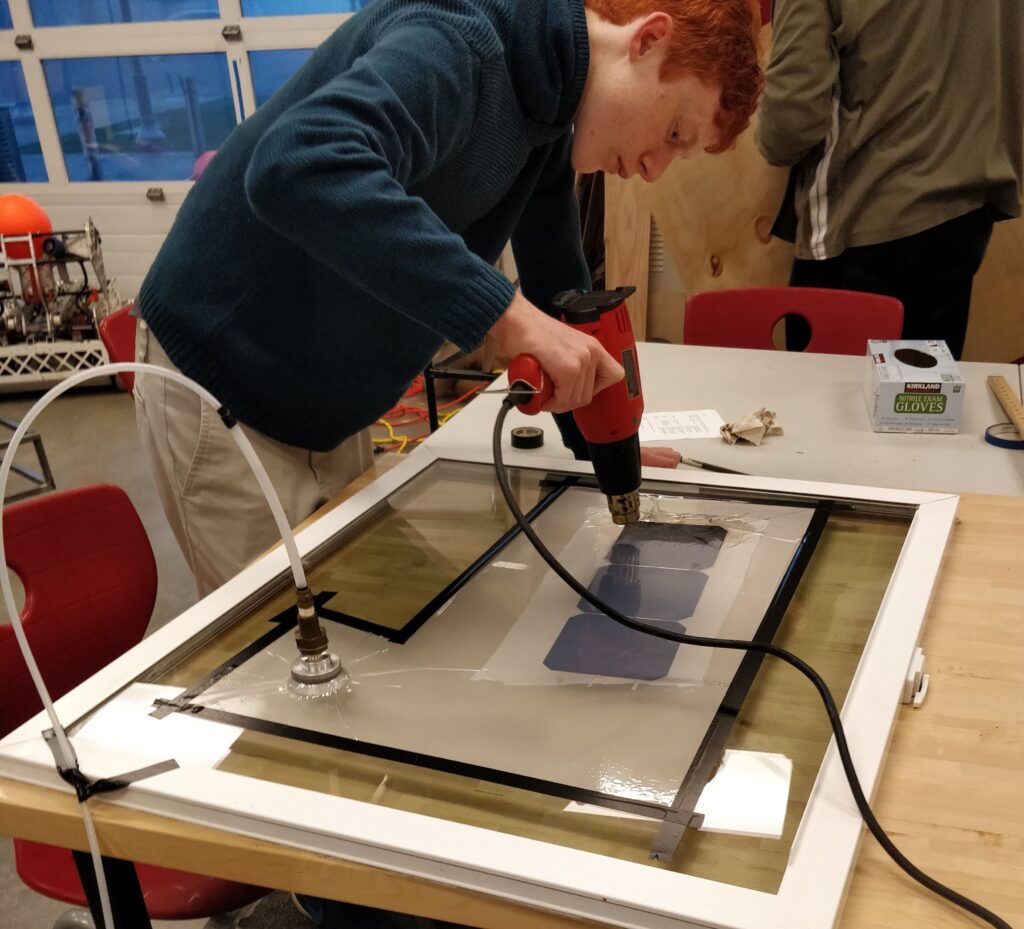
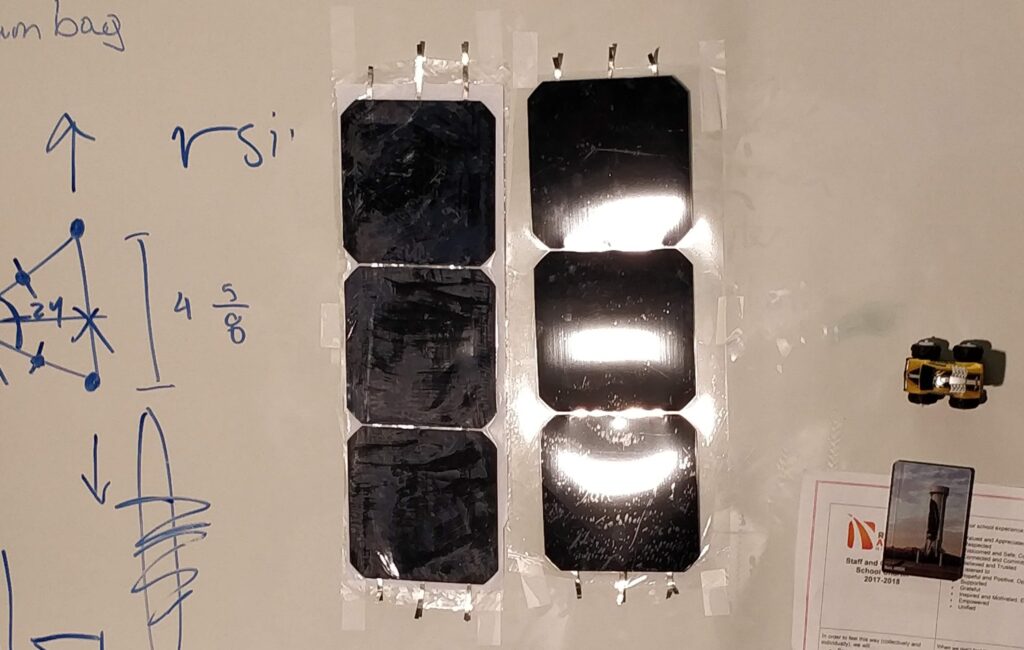
Power system circuits for solar array 1.0
I helped design and wire the main electrical connection that interfaced with the solar array. This included maximum power point trackers and safety components such as disconnect switches and fuses.

Aluminum frame for solar array
I helped design and construct the aluminum frame that supported the solar array. Aluminum was chosen for its light weight and stiff properties.
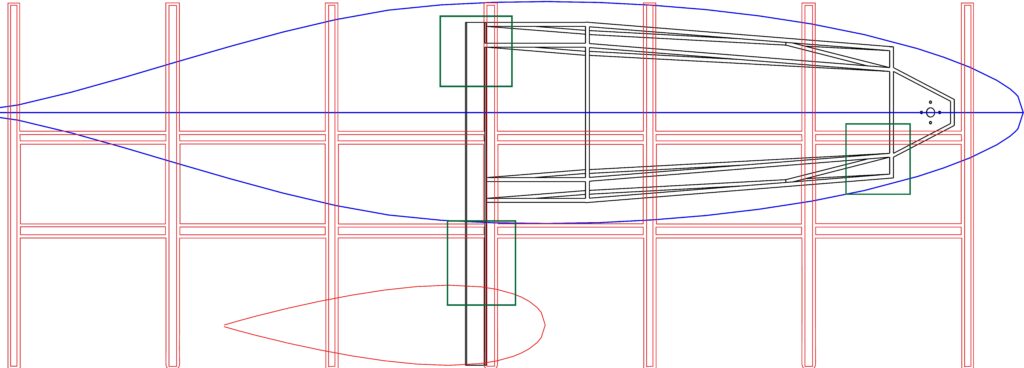
