Details
Turbulent premixed flames lie at the basis of gas turbines and various other technical combustion devices. Turbulence affects the rates of fuel burn by increasing the flame surface and increasing the rates of heat and mass transfer. Although fundamental questions of the scaling of turbulent flames with Reynolds number lie at the basis of effective design of combustion devices, the scaling of the flame surface and overall burn rates with the Reynolds number of the flow are not clear.
In this project, we set forth the goal of performing and analysis a set of Direct Numerical Simulations of canonical, laboratory-scale, lean methane/air turbulent premixed flames at 4 atm. The configuration consists of a slot turbulent flame whereby the incoming lean methane/air mixture of reactants are pre-heated to 800 K and the jet is surrounded by hot products of combustion, simulating a pilot.
The reactions are described by a reduced methane/air finite rate chemistry mechanism featuring 16 reactive scalars. We employ a massively parallel solver for the reactive Navier-Stokes equations in the limit of low Mach number. The equations are solved with a predictor-corrector strategy on up to 100,000 cores on the new Cray XC40 “Shaheen” available at KAUST.
We simulated 4 flames, all having the same bulk flow velocity, but different slot widths. In order of increasing Reynolds number, the flames feature Re = 2,500, 5,000, 10,000, 20,000. The simulations totalled about 60 M cpu hours. An additional simulation at Re = 40,000 is planned.
Below, the flame’s length is show to decrease as the Reynolds number is increased at constant bulk velocity. Note that all geometrical features are normalized by the slot width. As the Reynolds number of the flow increases, it is clear that small features appear in the flame sheet.
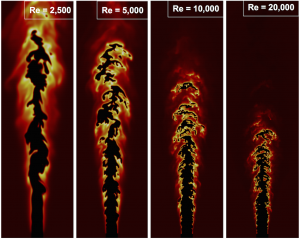
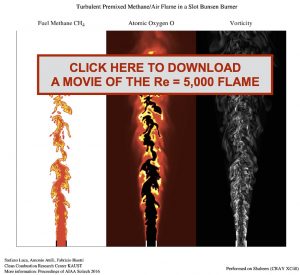