Bridging Gelation Kinetics with Architecture and Mechanical Properties of Elastomers
Polymer networks are essential in engineering and biomedical applications, such as elastomers in rubber tires, dampers, and seals; hydrogels in contact lenses and superabsorbent diapers; and pressure-sensitive-adhesives (PSAs) in labels, band-aids, and double-sided tapes. These soft, tough materials feature elastic moduli E ranging from 1 kPa to 1 MPa and can sustain large deformations near pre-existing defects or cracks.
However, at high temperatures or water concentrations, polymer networks readily fracture, limiting their use in applications such as water purification membranes, hydrogels for artificial prosthetics and drug delivery, solid polymer electrolytes for energy conversion and storage devices, and electro-adhesives for advanced manufacturing.10 Under these conditions, the polymer segmental dynamics facilitate ion or small-molecule transport, but the networks become prone to stress localization, crack nucleation, and fracture.
We aim to unravel design rules for polymer networks that remain soft and tough at high temperatures or water concentrations, leveraging recent advances in controlled polymerization methods, reactive Monte Carlo simulations, and polymer mechanochemistry to examine the relationship between network architecture, polymer chain breakge, and bulk fracture.
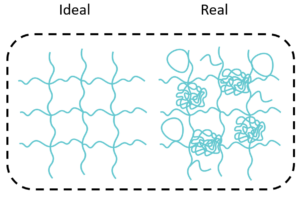

Painting a Multi-Scale Picture of Interfacial Fracture in Soft Adhesives
Numerous soft and tough materials have recently emerged, enabling advances in healthcare, energy, and manufacturing technologies, such as artificial prosthetics, wearable electronics, and soft robotics. However, understanding the deformation and adhesion of these materials remains challenging due to the critical role played by multiple length and time scales in the energy dissipation mechanisms ahead of an interfacial crack. These mechanisms include damage from reversible or irreversible scission and viscoelasticity from friction.
We aim to develop a multiscale understanding of interfacial fracture by unraveling the interplay between viscoelasticity and damage ahead of interfacial cracks. To this end, we leverage recent advances in polymer mechanochemistry with more conventional surface chemistry and mechanical testing to measure damage and aid in developing predictive models of interfacial fracture. These models could inform the molecular design of soft materials in emerging and increasingly demanding applications, such as wearable electronics, soft robotics, and reversible or bio-sourced bonds.
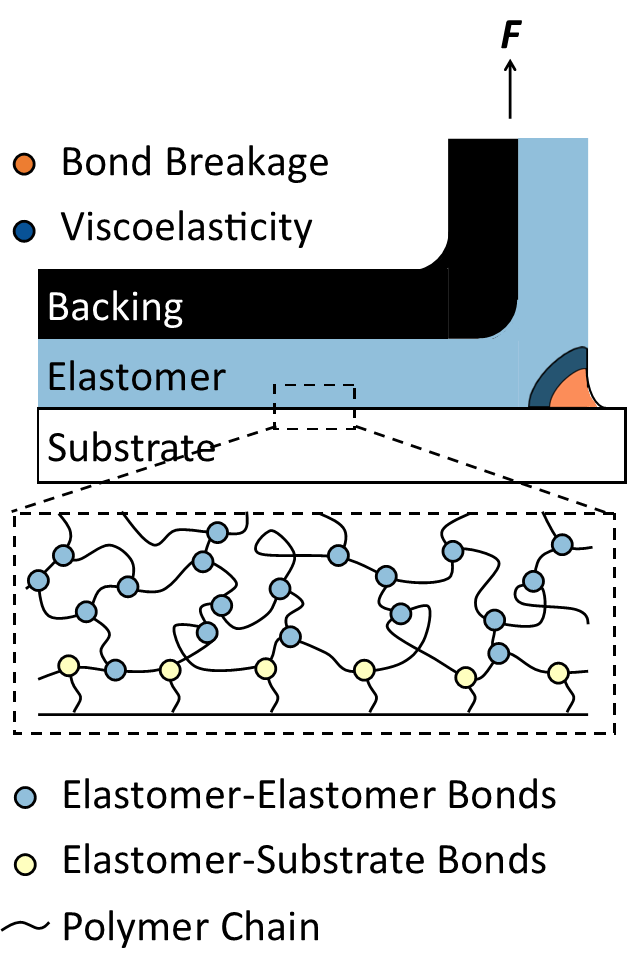

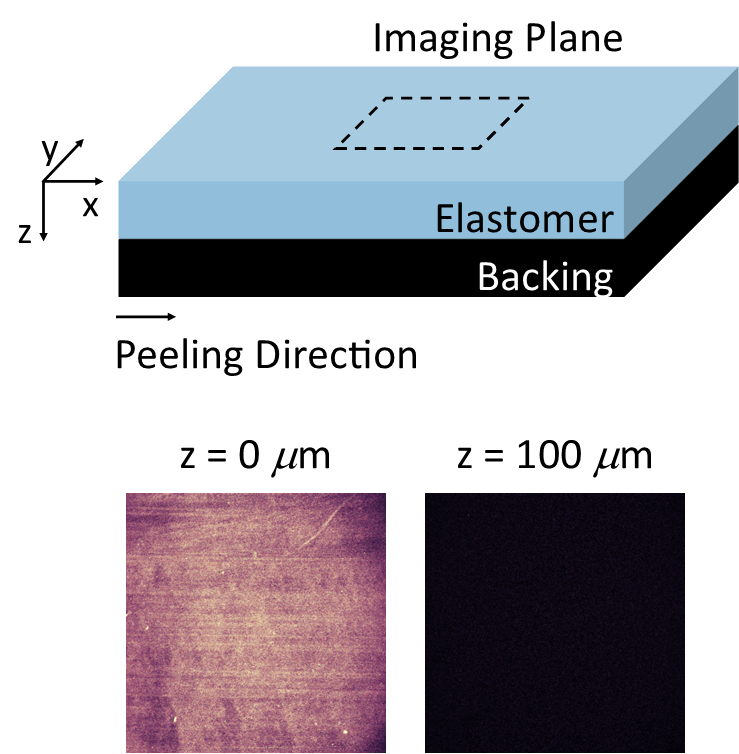
Co-Designing the Mechanical and Transport Properties of Membranes
Freshwater scarcity is an increasingly prevalent issue worldwide. Ultrafiltration (UF) membranes could play an important role in the solution but remain limited by a trade-off between their mechanical and transport properties. Their conventional manufacturing process, nonsolvent-induced phase separation, leads to kinetically arrested structures with a broad distribution of pores, which influence both the hydrodynamic resistance to water flow and the stress concentrations around the pores.
We aim to provide a molecular rationale for co-designing the mechanical and transport properties of UF membranes by leveraging solution self-assembly of block copolymers and architectures capable of delocalizing stress in bulk. If successful, our work should inform the molecular design of advanced UF membranes for emerging and increasingly demanding separations.