CFD Simulations of Multiphase Momentum Transfer Through Vapor-Liquid Contactors
- Sponsors: Eastman Chemical Company and Praxair
- Principal Investigator: Dr. Bruce Eldridge
- Graduate Research Assistant: Mikey Phan
- Status: In Progress
Motivation
This project involves the application of computational fluid dynamics (CFD) to traditional vapor-liquid contactor model development. The goal is to replace the empirical models currently in use with higher-level models that capture the underlying physics of the hydraulic and mass transfer processes. Ultimately, this rigorous framework will be used as a basis for more accurate predictive models which will 1) facilitate better operation and control of existing separation devices and chemical reactors, and 2) yield new equipment designs with lower capital and operating costs. This effort will incorporate results obtained from the Separations Research Program (SRP) pilot plant, X-ray CT images from prior DOE and NSF-supported research activities, and bench-scale CFD validation experiments.
In addition to advancing the state-of-the-art of gas and gas-liquid flow modeling, this research will optimize vapor-liquid contactor designs by developing a fundamental understanding of the hydraulic behavior of chemical process equipment. This optimization will be crucial to energy efficiency of separations and reactions in the chemical processing and refining industries and will be a prerequisite for effective vapor-liquid contactor design.
Approach
Minimizing pressure loss is crucial to high-flow-volume packing and catalyst bed applications. For this reason, the first step of this project is to create a converged gas-only model. A gas-only model will allow a detailed analysis of the mechanisms of pressure loss. As can be seen in Figure 1 from our previous efforts on structured packing, a contour plot of pressure can be generated on the surface of the packing. This allows for the immediate visual identification of packing features that contribute most significantly to energy dissipation.
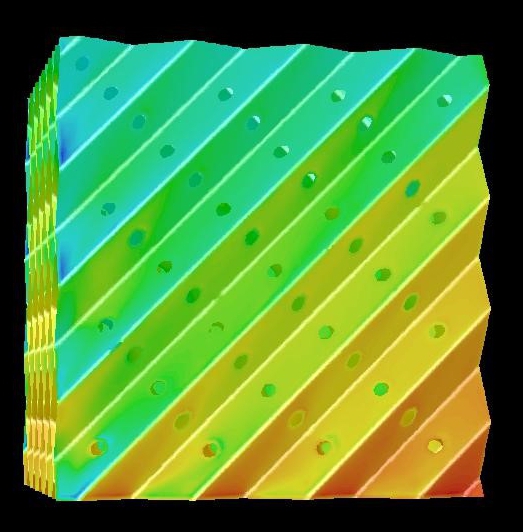
Geometry generation has long been a source of inaccuracy in CFD simulations. An electronic representation of the object in question is normally generated via computer-aided design (CAD) packages. Because the computer geometry is created from scratch, it omits fine features which are difficult to reproduce or are assumed to be irrelevant. By contrast, this project creates model geometry using X-ray CT scans (see Figure 2). High-definition 3D density maps are created by scanning the object many times from multiple directions. The resulting data accurately represents the object down to the spatial resolution of the X-ray detector (typically sub-millimeter). Consequently, exact representations are made of the packing without the need for simplifying assumptions. This project will take advantage of an ongoing collaboration with the University of Texas Computed Tomography (UTCT) Lab to produce high-fidelity, true-to-life CFD geometry. Scan data will be exported as a stereolithography (STL) file. The resulting data will exactly duplicate all packing features of 0.2 mm or larger. This file can be then imported directly to CFD meshing software.
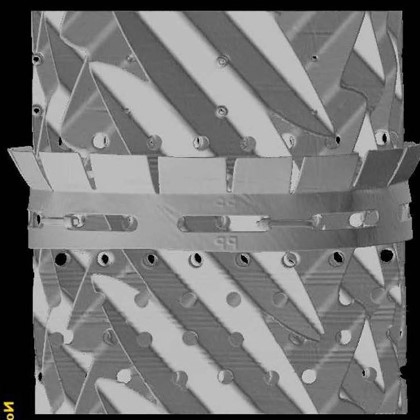
The Texas Advanced Computing Center (TACC), home of one of the most powerful supercomputers in the world, Stampede2, will provide the calculation resources. With a multitude of computing nodes available for distributed CFD analysis, highly accurate calculations can be completed in a relatively short amount of time. Moreover, the research staff at TACC represents a cross-section of leading scientists across many computational fields, including CFD. With these resources, both single and two-phase models are possible. Results obtained from different turbulence models will be compared to the experimental results to determine the most predictive approach. Grid/mesh sensitivity studies will be conducted to evaluate the trade-off between simulation accuracy and computational demand.
The results of this project will advance fundamental understanding of two-phase flows and the impact of fluid properties on flow evolution. With the recent advances in geometry creation and the computing power available at TACC, this understanding can be immediately applied to macro-scale equipment. This will produce an understanding of how fluid flow impacts the operation of a wide variety of multiphase unit operations inside the chemical processing industry. It will also allow for the optimization of equipment for energy efficiency resulting in a dramatic decrease in oil and gas demand.