Reactive Distillation in a Dividing Wall Column
- Sponsor: Eastman Chemical Company
- Principal Investigator: Bruce Eldridge
- Graduate Researcher: Jeff Weinfeld
- Status: Complete
Motivation
Reactive dividing wall columns (RDWCs) are highly integrated systems that can simultaneously perform chemical reactions and multicomponent separations within the same physical unit. While reactive distillation columns (RDCs) and dividing wall columns (DWCs) are becoming increasingly popular in chemical processes due to their ability to present significant costs and energy savings, RDWCs have not been commercially adopted. RDWC research has been an active area of research only over the past decade, with studies concluding the technology is industrially feasible. The goal of this project is to increase current knowledge of RDWCs to better evaluate their commercial potential and provide insight into their optimal design. This will be done by operating a bench scale RDWC, developing and validating a rigorous RDWC model, and then using the model to further investigate important RDWC variables.
Background
Distillation is the most common method of chemical separation. As of 2010, there were reportedly 40,000 distillation columns operating around the world 1. However, it is an energy inefficient operation and it has been estimated that together these columns consume approximately 3 percent of all energy worldwide 2, and up to 80 percent of energy in chemical plants 3. As a result, a focus of distillation research has been to save energy, and therefore money in chemical processes by increasing the efficiency of columns.
The dividing wall column (DWC) is a non-conventional distillation column that has become a popular example of process intensification. Introduced by Wright in 1949 4, the DWC performs multicomponent separations that normally require multiple distillation columns, in a single piece of equipment. This is achieved through the unique feature of a DWC, a partial vertical partition that exists inside of the column. On the feed side of the dividing wall, the high and low boiling components are separated, while the middle boiling components are split to both the top and bottom of the wall. On the product side of the dividing wall, the middle boiling components are then separated from both the high and low boiling components and withdrawn from the column as a side product. Therefore, the DWC essentially combines the separation ability of two different distillations columns into a single unit. A DWC and its equivalent conventional process is shown in figure 1.
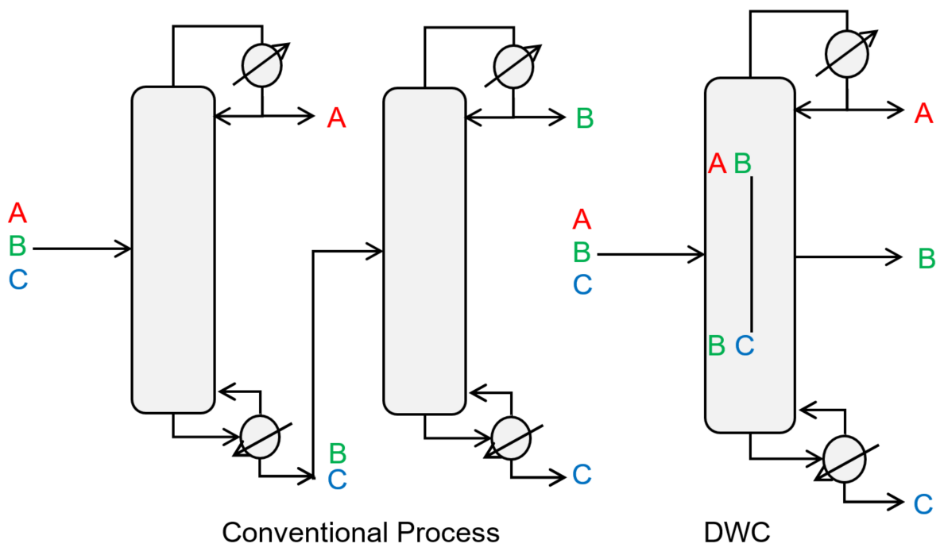
There are many energy and cost savings advantages of integrating two distillation columns into a DWC. Since one column is now required instead of two, there are significant installation cost savings, despite the slightly larger diameter typical of DWCs. Similarly, operating costs are reduced as only one reboiler is required in a DWC. Additionally, the DWC has a higher thermodynamic efficiency than multiple column processes since the middle boiling components are no longer forced to remix with other components. In chemical plants with limited space, the reduction of plant area required is another advantage. Despite its advantages, the DWC does have some limitations. The column can only operate at one given pressure and reboiler duty, therefore decreasing the operational degrees of freedom compared to a multiple column sequence. The reboiler duty also must be able to supply all the heat to the entire process, and the condenser must withdraw all the required heat of evaporation for the process. However, studies indicate the advantages of DWCs outweigh its drawbacks, and it can produce significant energy and costs savings.
DWCs have been studied extensively in literature, with papers covering a wide range of subjects and chemical systems. Topics covered include shortcut design methods, rigorous steady state simulations, dynamic control simulations, experimental operation at both pilot and industrial scale, and column hardware. A number of reviews of DWCs have been published 5-9. These works conclude that DWC modeling, design, and control is feasible with 25-40 percent energy savings and 30 percent lower investment costs compared to traditional processes. As a result, DWCs have received considerable attention from industry. Due to varying definitions and lack of industrial disclosure, the total number of DWCs used in industry is unknown. However, it has been estimated that there are at least 125 operating DWCs, with over 70 units belonging to BASF 8. DWCs clearly represent a successfully first level process integration.
Another first level process integration scheme that fits within the guidelines of process intensification is reactive distillation (RD). First patented in 1922 by Backhauss 10, reactive distillation columns (RDCs) are traditional distillation columns in which a reaction occurs, therefore combining reaction and distillation into a single unit operation. By doing this, the products of the reaction are formed and separated simultaneously. A RDC and its equivalent conventional process is shown in figure 2.

Similar to DWCs, RDCs have many advantages associated with the integration of unit operations, and also a few disadvantages. Installation costs are reduced, since a reactor vessel is no longer needed. Because the products of a RDC are also the products of a chemical reaction, their removal can partially shift equilibrium toward additional product formation, therefore increasing conversion and selectivity. Additionally, in an exothermic reaction, heat released from the reaction will reduce the amount of required reboiler duty. Further advantages are the stabilization of reaction temperature by elimination of catalytic hot spots, and the breaking of azeotropes in the chemical system through reaction. The main disadvantage of RDCs is that the amount of catalyst, residence time, and reaction conditions all must be compatible with the separation requirements. Similar to DWCs, further integration can make control more difficult. However, the advantages of RDCs can outweigh the disadvantages and this technology has been successfully implemented in industry.
While it was first patented nearly a century ago, significant commercialization of RDCs did not occur until the 1980s 11. Design of RDCs is more complex than DWC design, as modeling the reaction location and properties can be difficult, and since parameters such as catalyst loading, liquid holdup, and feed location can have a major impact. Researchers have studied a wide range of systems dealing with various areas such as modeling, shortcut and rigorous simulation, experimental operation, and control. The current body of work on RDCs totals over 1100 articles and 800 US patents covering over 235 reaction systems 8. Detailed reviews of RD processes can be found in published literature 8,11,12. Conclusions are that modeling and experimental operation are feasible with over 20 percent savings in energy requirements and capital costs being typical when compared to the traditional process of a reactor followed by a distillation column. It is difficult to estimate the number of RDCs in industry, but it is worth noting that CDTECH, the major commercial RD technology provider, has licensed over 200 commercial scale processes worldwide as of 2010 8.
Taking integration one step further, reaction and multicomponent separation can be combined into a single piece of equipment, known as the reactive dividing wall column (RDWC). This column can be thought of as either a reactor integrated with a DWC, or an RDC integrated with a standard distillation column. While Kaibel first mentioned the opportunity to carry out a reaction in a DWC in his 1984 patent 13, RDWCs were not modeled until 2004 14, and experimented until 2007 15. To date, there are over around 50 published articles on RDWCs covering topics such as experimental operation, shortcut modeling, rigorous steady state modeling, and dynamic control. Despite this body of literature, gaps in knowledge required for industrial operation are limiting RDWCs’ commercial adoption. RDWC research is currently very active with over a third of these studies being published in just the past two years. The primary conclusion is distillation can present significant energy and cost savings and does have an industrial future. A RDWC and its equivalent conventional process is shown in figure 3.
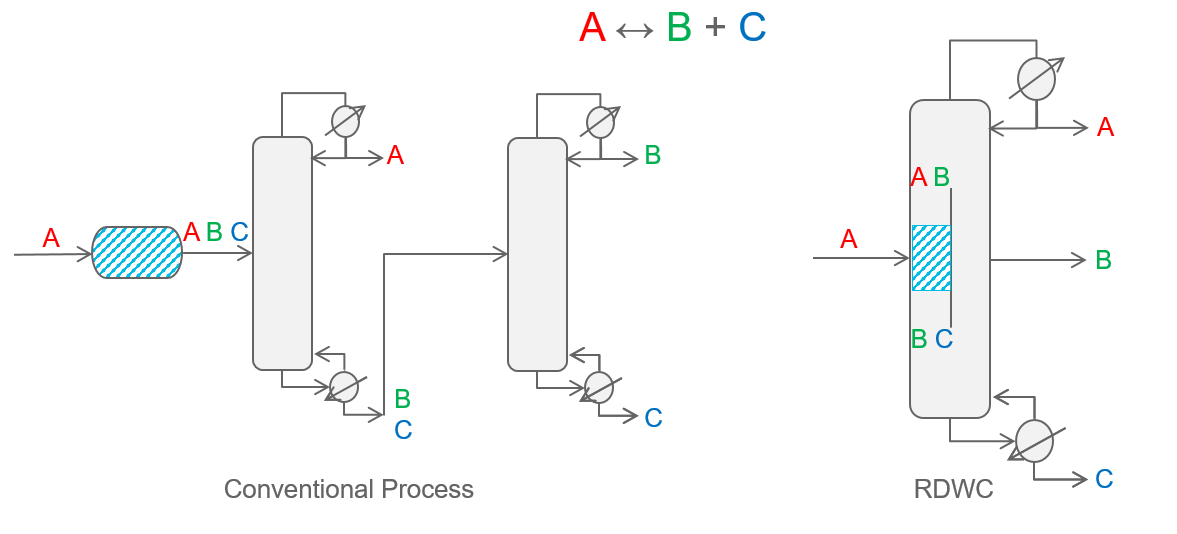
The lack of recent studies can be attributed to the complexity associated with RDWCs in addition to its emergence as an area of distillation research. RDWCs are more complex than RDCs or DWCs due to their large number of design and operational variables. When a wall is inserted into a conventional distillation column to yield a DWC, the height and axial location of the wall must be specified. From an operational view, the liquid split to each side of the column from above the wall can have a significant impact on column performance. The vapor split from the section below the wall can also impact column operation, but is difficult to control in practice. When a conventional column is transformed to carry out a chemical reaction, either a heterogeneous or homogeneous catalyst must be chosen. If heterogeneous, the catalytic packing, as well as its placement in the column must be specified. Therefore, if a heterogeneous reaction is carried out in a RDWC, both the catalyst and packing arrangement, as well as the wall location must be specified. The introduction of catalytic packing into one side of the column can lead to further complexity since the different packing configuration will lead to a difference in pressure drop between both sides of the column. This impacts the vapor split and causes it to not be proportional to the ratio of the cross-sectional areas on each side of the wall. Figure 4 shows design and operational variables to illustrate the high level of complexity in a RDWC.
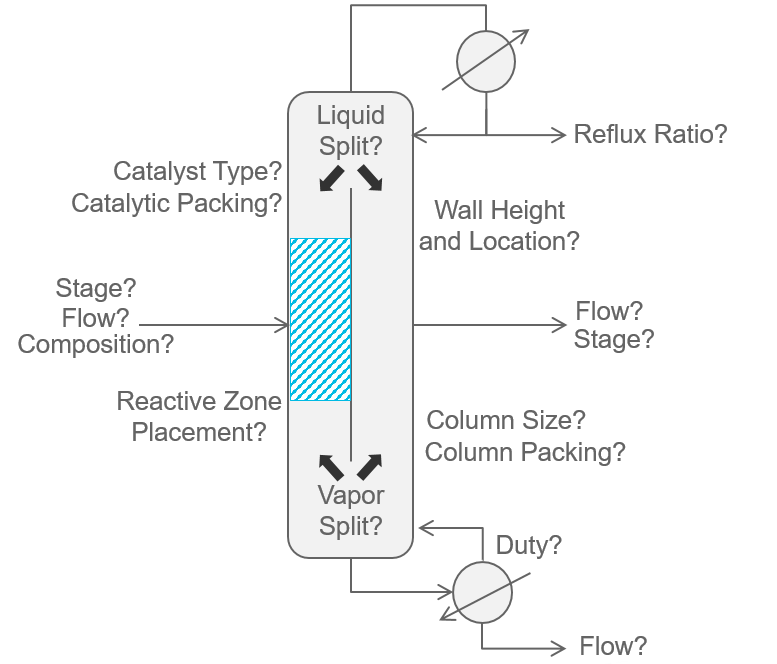
Completed Work
A test system was chosen for the project. Kinetic and phase equilibria data of the system is essential to modeling reactive distillation and designing a RDWC. Therefore, due to the lack of such data for the system in literature, a series of kinetic and phase equilibria experiments were designed and completed so that the data could be determined experimentally. Using this information, a simplified reactive distillation sequence was designed and constructed on the laboratory scale to ease the eventual transition to a dividing wall column. An experimental campaign has been completed on the reactive distillation unit to provide steady state data that was used for modeling and design purposes.
Sources
(1) Diggelen, R.; Kiss, A.; Heemink, A. Comparison of Control Strategies for Dividing-Wall Columns. Ind. Eng. Chem. Res. 2010, 49, 288.
(2) Nguyen, N.; Demirel, Y. Using Thermally Coupled Reactive Distillation Columns in Biodiesel Production. Energy 2011, 36, 4838.
(3) Bumbac, G.; Ene, A.; Isopescu, R.; Toma, A. Process Simulation of Reactive Distillation in Dividing Wall Column for ETBE Synthesis Process. Chem. Eng. Trans. 2009, 18, 487.
(4) Wright, R. O. Fractionation Apparatus. US2471134 A, May 24, 1949.
(5) Asprion, N.; Kaibel, G. Dividing Wall Columns: Fundamentals and Recent Advances. Chem. Eng. Process. Process Intensif. 2010, 49 (2), 139.
(6) Dejanović, I.; Matijašević, L.; Olujić, Ž. Dividing Wall column—A Breakthrough towards Sustainable Distilling. Chem. Eng. Process. Process Intensif. 2010, 49 (6), 559.
(7) Yildirim, O.; Kiss, A.; Kenig, E. Divided Wall Columns in Chemical Process Industry: A Review on Current Activities. Sep. Purif. Technol. 2011, 80 (80), 403.
(8) Kiss, A. A. Distillation Technology – Still Young and Full of Breakthrough Opportunities. J. Chem. Technol. Biotechnol. 2014, 89, 479.
(9) Donahue, M. M.; Roach, B. J.; Downs, J. J.; Blevins, T.; Baldea, M.; Eldridge, R. B. Dividing Wall Column Control: Common Practices and Key Findings. Chem. Eng. Process. Process Intensif. 2016, 107, 106.
(10) Backhaus, A. A. Apparatus For The Manufacture Of Esters. 1,425,624, August 15, 1922.
(11) Segovia-Hernández, J. G.; Hernandez, S.; Petriciolet, A. B. Reactive Distillation: A Review of Optimal Design Using Deterministic and Stochastic Techniques. Chem. Eng. Process. Process Intensif. 2015, 97, 134.
(12) Sharma, N.; Singh, K. Control of Reactive Distillation Column: A Review. Int. J. Chem. React. Eng. 2010, 8 (1).
(13) Kaibel, G. Destillationskolonne Zur Destillativen Zerlegung Eines Aus Mehreren Fraktionen Bestehenden Zulaufproduktes; Google Patents, 1984.
(14) Kenig, E. Y.; Mueller, I.; kloeker, M. Rate Based Modeling of Dividing Wall Columns – a New Application to Reactive Systems. In Proceedings of the PRES 7th Conference; 2004.
(15) Sander, S.; Flisch, C.; Geissler, E.; Schoenmakers, H.; Ryll, O.; Hasse, H. Methyl Acetate Hydrolysis in a Reactive Divided Wall Column. Trans IChemE 2007, 85 (A), 149.