This essay is part of a slow research series, What is Research?
Our work in the Harry Ransom Center’s Preservation and Conservation Division focuses on caring for the Center’s vast and varied collections. Much like the interdisciplinary nature of today’s engineering and medical professions, science, technology, and craft underpin the work of the division’s conservators and preservation technicians. While our work as preservation technicians focuses heavily on preventive actions such as integrated pest management and monitoring the storage and exhibition environments, we also design and construct protective enclosures to safeguard collection objects, photographs, books, audiovisual recordings, works on paper, and more.
In many ways constructing specialized enclosures is akin to engineering; we improve upon the materials used and structures developed by our predecessors. Sometimes a collection requires us to develop a wholly new design, requiring a research process based on understanding the physical nature of the object and its use, design development, specification of materials, and enclosure construction. Housing the production art in the David O. Selznick Collection is a case in point.
Selznick was a movie producer during the 1930s, 40s, and 50s at MGM, Paramount, RKO, and at his own company, Selznick International Pictures. His archive spans 50 years, from 1916 to1966 during which time he produced such films as A Star is Born, Adventures of Tom Sawyer, The Third Man, Gone with the Wind, Rebecca, Notorious, and Spellbound. The storyboards and production art created for these films are requested by researchers and scholars, displayed for tours and classes, and often exhibited.
The Selznick Collection, one of the largest and most frequently sought out collections at the Ransom Center, is vital to the research and study of the Golden Age of Hollywood and the history of American cinema. It represents a massive collaboration of writers, directors, performers, musicians, art directors, and designers. These movies remain important to those interested in American culture; they are re-examined and critiqued, again and again.
Acquired by the Center between 1981 and 1995, the collection contains hundreds of storyboards –large, hand painted illustrations of various visual aspects of filmmaking, including film sequences, costumes, actors, set design, scenery, and exterior locations.
These storyboards had never been surveyed for preservation to determine what protective housings would best serve their storage needs as well as their consultation by researchers in the Center’s Reading and Viewing Room. Due to the size and scope of the collection, the delicate nature of the items, and their popularity and research value, our team of three preservation technicians—Alan Van Dyke, Jill Morena, and I—had the exciting opportunity to find an innovative solution to preserving this extraordinary collection.
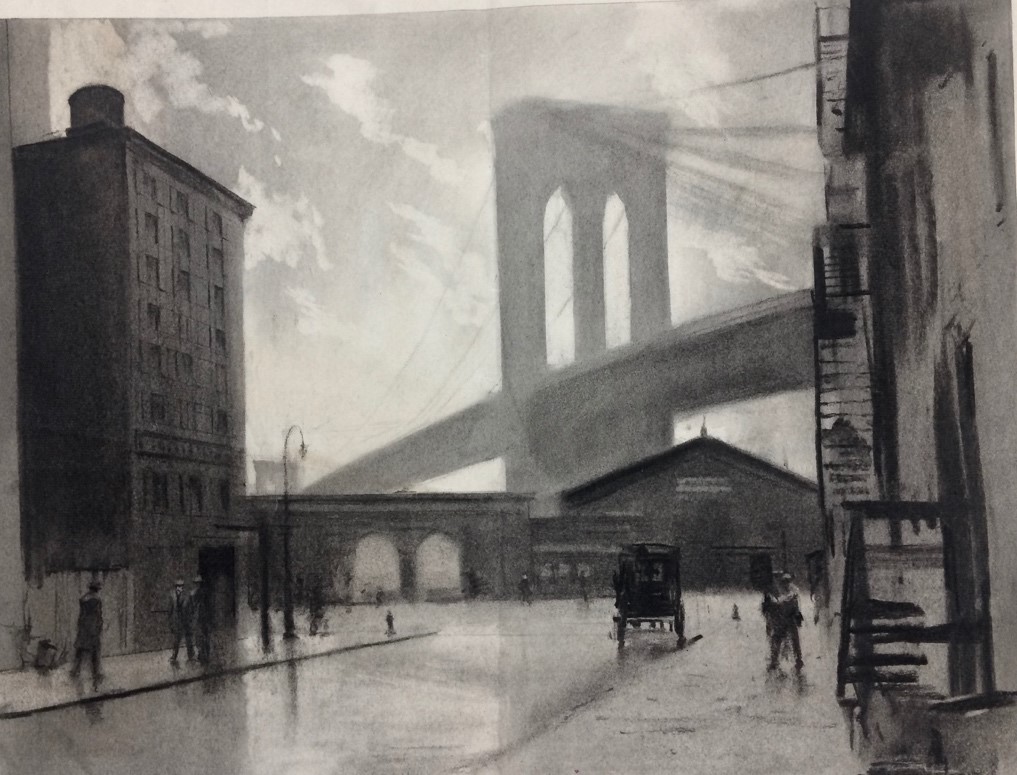
Throughout 2018, our team rehoused over 300 of these fragile storyboards. The project involved a comprehensive survey and yielded an inventive new housing design and workflow model. Although this sort of project might not fit the mold of traditional research, our process of engineering housings mirrors the process of research: from analysis to design development, assembly, refinement, editing, and evaluation of the final structure in practice. In that sense, it is research of a material nature. It becomes a model on which to base future projects, joining other new systems and structures that slowly enter our preservation canon: an assembly of designs tested, retaught, shared, and adapted through the years.
Our first step in this process was to conduct an extensive survey of the storyboards through the lens of preservation. We examined each piece and recorded measurements, support type, media type, general condition, and issues such as losses or cracks. Most of the 300 objects are paintings and illustrations in watercolor, graphite, or charcoal. All of the media are prone to cracking and flaking, fading, or smudging. The friable nature of the media is a particular reason that the housing had to be well thought out and sufficiently protective. Moreover, many of the storyboards don’t lie flat and are bowed to some extent, which further complicates their safe housing. These issues required that we develop a new kind of protective enclosure.
We settled on a sink mat structure, fabricated out of archival grade corrugated board, a material that is extremely light and strong and easily transported in and out of collections storage. A traditional “sink mat” is a custom-made protective enclosure that supports an object with a frame where the walls of the sink come to the edge of the object. With our sink, however, the walls function as a structure within which the object can sit, protecting the fragile surface of the painting or graphite illustration and accommodating any bowing or planar irregularities of the support itself. This construction provides sufficient depth so that the hinged “lid” of the enclosure won’t touch the illustration media.

Workflow analysis helped to further crystalize the design and construction. Designing our workflow entailed allotting time for cutting out and assembling the pieces, planning for repetitive, high-quality construction, while ensuring good ergonomics for the technicians. In the early stages of the project, we built in time for the paper conservators and curator of film to provide feedback. While similar to traditional research, in our case we materialized concepts in three-dimensional structures. Our editing process happened with board and glue, borne out with many models tested for durability, functionality, and practicality.
Fabricating the housings was more or less assembly-line work to maximize time and energy. We made 300+ sink mats with a goal that each protective “box” would be customized to the piece, and would facilitate access. Although we couldn’t at all be sloppy with this process, it was relatively easy to glue up walls to the support boards and to hinge on cover lids. We weren’t dealing with the delicate objects at this point, just putting the sink parts together. All told, we assembled 600 pieces of support board, 2400 2” walls, and cut and folded 2400 Permalife paper corners—and consumed many, many podcasts. Once we finished the assembly-line work, we turned our attention to customizing each sink mat for its specific storyboard. We measured each piece for its tailored sink mat, pasted in custom corners to hold the board in position, and carefully transferred each storyboard into its new home.

Building hundreds of sink mats in a short amount of time offered a new precedent in our housing work. Sink mats are now one of our standard boxing options, alongside tux boxes, phase boxes, drop front boxes, and folders. The pattern is now so well ingrained that our technicians can easily build, design, and tailor sink mats. A huge benefit to a mass-production project like this is that it instills muscle memory and allows us to refine a pattern.
Because we’ve discovered mistakes and pitfalls in previous projects, we also (hopefully) can keep those mistakes in mind to create more accurate and efficient projects in the future. An extensive survey at the beginning of the project helped us keep our thinking flexible and gave us time to develop a human-based workflow focused on open and fluid communication among the technician team, tailoring timelines around each person’s range of responsibilities. In the final analysis, the new enclosure structure greatly improves preservation of and accessibility to the storyboards. Now logically organized and labeled in flat file cabinets, the Reading and Viewing Room paging staff can locate and transport a storyboard with ease.

Our work in the Preservation and Conservation Division combines analysis of the object and, sometimes, material engineering. I would make the argument that the craft aspect of our work embodies the spirit of research, if not outright replicates it in material form.
We spend years thinking about objects and how they move through space and time: who uses them and how. Conservators and technicians are constant observers of objects. With regard to protective housings, our goal is to develop and refine our structures to better “outfit” and protect cultural records from wear and natural aging.
We revisit our structures and constantly rework and refine them. Craft is a process of development, design, assembly, and adaptation for real-world function. Once our designs are in the world, we get to observe their efficacy in real time. The process builds a canon of design and structure that an institution or field can accept as standards. This is research in practice!
Further Reading
Adamson, Glenn. 2013. The Invention of Craft. London: Bloomsbury.
Cunningham-Kruppa, Ellen. Mooring a Field: Paul N. Banks and the Education of Library and Archives Conservators (Legacy Press, 2019).
Northeast Document Conservation Center. 2015. “NEDCC Preservation 101: NEDCC Preservation Leaflets.” https://www.nedcc.org/free-resources/preservation-leaflets/overview
Phibbs, Hugh. 1997. “Preservation Matting for Works of Art on Paper.” Library of Congress. (Originally published in Picture Framing Magazine, Feb 1997. https://www.loc.gov/preservation/care/Phibbs.pdf